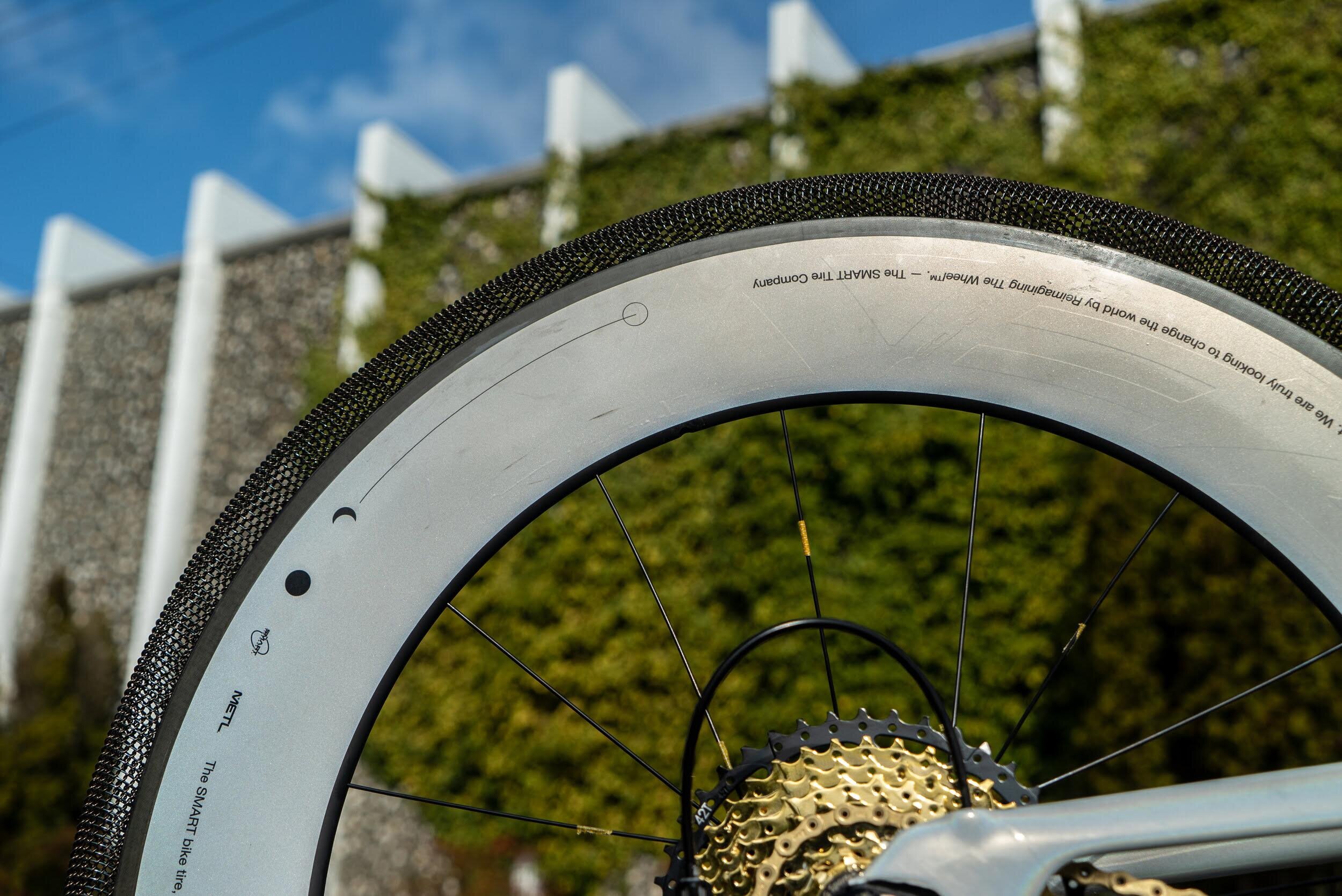
SMART FAQs
How much do these tires cost?
Our initial cycling products will be more of a premium within their markets, comparable to a high performance or racing tire (full purchase and subscription model available). This is due primarily to the high cost of NiTinol. We have identified several R&D goals related to dropping our material costs by up to 90%. In addition, there is intense ongoing research at the laboratory stage involving comparable materials that are ~80% cheaper than NiTinol. We are actively engaged with some of these researchers, and plan to be early adopters as we build our economical supply chain and manufacturing process.
We are also developing advanced automotive and trucking tire prototypes, with a goal of disrupting and competing with the old formula set up by the major tire manufacturers. We plan to usher in a new era of sustainable transportation with cleaner, safer, longer-lasting tires, that are price comparable to branded tires currently on the market, saving consumers much more money in the long run. Now, that’s SMART.
How far along are you? When can I buy a set of METL™ tires?
The technology has been developed for 7+ years at NASA Glenn Laboratory, with a budget of several million dollars. We are at an advanced prototype phase, where product has been tested on rovers, automobiles & bicycles. We've chosen to develop a bicycle tire as our first product, as a way to put this incredible technology directly into consumer hands and spread awareness of the benefits. We expect to launch our METL™ product in Q3 of 2024.
Who competes with you? What do you understand that they don't?
Our direct competitors are the major tire manufacturers (Bridgestone, Michelin, Goodyear, etc). No competitor is equipped to produce shape memory alloy tires. The technology is patented & the manufacturing process is significantly different. Materials experts are in extremely short supply; in this case practically only at NASA. Lastly, the business model is different. 70% of tire sales are replacements, and companies are not genuinely focused on a sustainable model. We believe our customers want safer, maintenance-free tires that challenge the status quo. Similar to how Tesla took on the electric vehicle market over 17 years ago, we are here to reinvent the tire.
Will these tires have rubber treads?
On Mars, no. On earth, yes (unless you want to put these on a dune buggy). SMART tires are designed for use on the same terrain as a conventional tire, and will be integrated with a new, long-lasting, rubber tread. What is different about our type of rubber integration:
Our tires will be re-treadable! This is a ground-breaking design and proprietary system still in development, but will save consumers time and money. Instead of replacing a whole tire after a flat, imagine never getting a flat, and only having to replace the layer of rubber tread when that wears out, always keeping the original tire structure throughout the life of your vehicle.
Since the tire is airless, and provides its own load bearing elements, we don't need sidewalls except for aesthetics and to keep debris out of the tire. This means less rubber used, less tire waste, and and a tire that is better for the environment.
We favor long-lasting treads, to continue the theme of long-lasting, low maintenance tires. Our chief engineer is a former principal engineer at Goodyear Tire & Rubber Company, who is optimizing a specialized formulation for the ultimate tread grip, durability and long life.
The SMART tire can last the life of your vehicle/bicycle, but eventually the rubber-like tread will wear down and can be re-treaded within our recycle system. It’s a lot better and cost-effective than having to buy a brand new set of tires.
What happens when the tread wears out? Do you recycle the NiTinol?
While we expect to deliver industry-best tread wear, eventually any tread needs to be replaced. The closest comparison is the trucking industry, in which re-treads enable extreme mileage on a single tire before it reaches end-of-life. Unlike trucking, we expect our structural tires to last through many retreads. In practical terms, this means the tire can live as long or longer than the vehicle it was originally purchased for. All materials eventually incur damage and need to be repaired or refurbished. While the NiTinol shape memory alloys we use are extremely resilient, we are developing two main pathways to reuse:
Mechanical repair, by reshaping and heat treating localized damage, or replacing individual elements.
Material recycling: melting recycling as part of our NiTinol supply chain.
How much do these tires weigh? Isn't metal heavy?
Metal is in fact, heavier than air; however, these tires are comparable with many mainstream alternatives when it comes to weight. This includes gravel & mountain bikes, eBikes, automotive tires and truck tires. This does not count externalized savings such as tire pressure monitoring systems, or spare tires and inner tubes. This is possible due to several key factors:
SMART Tires remain mostly empty and are highly optimized for this application. Picture an inner tube, or radial arcs that provide structural support. Much like graphene, a more well known "super" material, the properties of NiTinol are much greater than common metals such as steel, or even ordinary titanium.
Conventional tires us an excess of rubber in order to retain pressure and carry heavy loads: the higher the load, the thicker the rubber. They are MUCH more than just treads. They also use steel belts, beads and other reinforcements that are just as heavy as NiTinol. Our tires are made with less than half the rubber used for conventional tires.
NASA is really good at structural engineering. When designing these structures for missions on far away planets, payload is incredibly important. Not a gram is wasted, and the same is true for SMART tires on Earth.
What is SMART’s relationship with NASA?
The SMART Tire Company (STC) is a commercial licensee of NASA’s superelastic tire technologies, which include the lunar/Mars spring, radial stiffened & SMA tubular structure patents, covering a diverse set of terrestrial and extraterrestrial applications using shape memory alloys and other materials. Additionally, STC has a Space Act Agreement with NASA to further develop this tire technology for commercial use with assistance from engineers and scientists at NASA Glenn Research Center in Ohio.
Where and how are these tires made?
All of our products are made in the USA - in Ohio, Indiana and California. Our shape memory alloy components are developed and manufactured in Indiana by a NASA-experienced metal manufacturing company. Cleveland, Ohio is home to the American rubber & tire industry, and NASA Glenn Research Laboratory. Strategically located in the heart of the Rust Belt, Cleveland sits between the centers of the automotive and metal industries. This is where we plan to scale our major manufacturing operations. Our product design and marketing operations are based in California, which is also home to our METL collaborators, Spin and Felt Bicycles.
Why a bicycle tire? If this technology is so great, shouldn't you be targeting automotive, trucking and aerospace?
We're building a bicycle tire first, because it allows us to build core capabilities and put an extremely cool product in people's hands more quickly. That said, everything we are doing to develop our METL™ bike tires, is part of a greater strategy to mass market SMART tires. Also, we just think it's a really great product that speaks for itself.
As part of our commercialization strategy, we conducted dozen of customer interviews across industries from ATVs, construction, agriculture, EVs, long-haul trucking, military, electric scooters to aerospace and even desert truck racing and wheelchairs. We priced different designs and tire sizes, examined regulatory requirements, and with few exceptions, there is very high potential in many market segments. Out of all these opportunities, cycling came in 1st, but it's worth knowing a few things about the future potential:
Future autonomous vehicles are heavier, and need longer lasting tires. We've already tested a radial prototype on a Jeep.
Trucking understands the ROI on a superior tire like nobody else. They track fuel efficiency, downtime & lifetime maintenance costs to the penny. We have already received interest from 2 of the top long-haul trucking companies in the US.
Aerospace. Imagine the forces exerted on the landing gear of a 737 jet. Now imagine cutting 100s to 1000s of pounds of payload, because you no longer have super heavy duty tires inflated to 200 PSI. That kind of weight savings is the holy grail of aerospace innovation, and also aligns with the recent development of the first all-electric aircraft.
I'm a cyclist, but I'm skeptical. Is the ride really smooth, and is it safe?
Our 1st prototype was built to simulate a standard pneumatic road bike tire (700c) at a tire pressure of 100 PSI. It was installed in tandem with the pneumatic tire on the *same* bike and taken for a test ride. This was the moment that caused so much initial excitement around METL™! The difference between the tires was not noticeable, despite being two different models. We're currently finishing our 3rd generation prototype (gravel) based on initial feedback, and will be in the lab with NASA modeling precise properties prior to product launch, to ensure the best possible riding experience. As a structural tire firmly fastened to the wheel rim, we consider these tires to be extremely safe. Unlike a pneumatic tire, there is no possibility of losing air pressure, and folding around corners is also very unlikely. Depending on the model, they can also operate with a flatter footprint for increased traction.
How can a tire be eco-friendly? Is that good for business?
The tire industry is incredibly dirty. Tires are made from petroleum products, carbon black, plastics and metals. Then they wear out and are recycled or disposed: as in, 50 billion pounds per year buried or burned. Even worse, recent research shows that 20-30% of ALL ocean microplastics come from ordinary tire wear that is washed off of our roads and into our waterways. We can't solve all of these problems, but we can make a big difference. Tires don't have to be disposable. Small improvements to something as fundamental as the tire have huge ripple effects. Better fuel efficiency. Less rubber produced (we use 50% less rubber for our tires). Tougher treads that shed less plastic.
The SMART Tire Company is a for-profit business so we won't be making hemp tires (though if someone knows how to do that- please call!). However, a more renewable tire is good business that has huge value across many market segments. It just hasn't been done successfully before. As founders, we're committed to nothing less than global impact, and to do that we need to both succeed commercially AND address some of the issues head-on. When Tesla first took the plunge into EVs over 17 years ago, they set the standard in eco-conscious transportation. We humbly follow their lead into the tire industry.
What is METL an acronym for?
Martensite Elasticized Tubular Loading. Martensite is a very hard form of steel crystalline structure. When a shape memory alloy is in martensite form at lower temperatures, the metal can easily be deformed into any shape. When heat-treated a certain way, the martensite reverts to austenite, and the material recovers its original shape, giving it super-elastic properties. We designed this in tubular form for bicycle tires.